ICT offers wide variety of parts (balls, rings and cages) in small batches.
Components for bearings used in aircraft applications need to meet high standards of quality, reliability, and performance due to the critical role they play in ensuring the safety and functionality of aircraft. Here are the main characteristics and requirements for components like balls, rollers, rings and cages used in aircraft bearings:
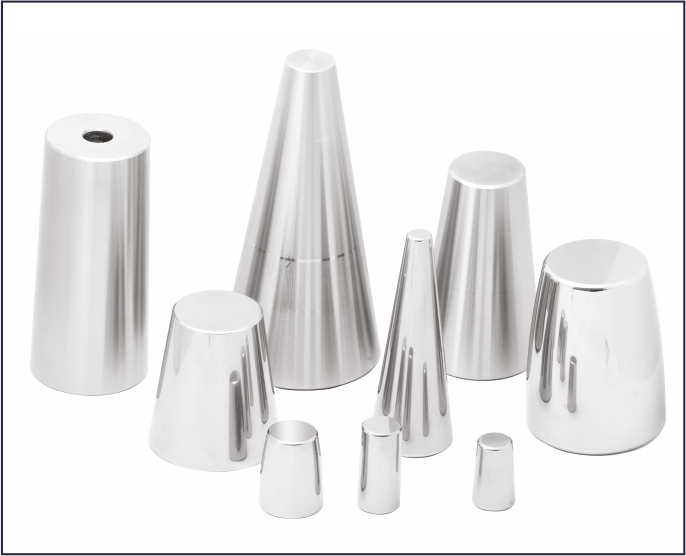
- MATERIAL SELECTION: Aircraft bearing components are made from high-quality steels and specialty alloys, all materials that are chosen for their strength, corrosion resistance, and durability in extreme conditions.
- PRECISION MANUFACTURING: Each part must be manufactured with extremely tight tolerances and precision in order to ensure that bearings operate smoothly and with minimal friction, reducing wear and tear.
- SURFACE FINISH: The surfaces of balls and rings raceways must have a smooth and uniform finish to minimize friction and reduce the risk of damage to the bearings.
- HARDNESS: High degree of hardness is necessary to withstand the loads and stresses that components encounter during operation: heat treatment processes such as carburizing or nitriding are often used to achieve the required hardness.
- LOW WEIGHT: Reducing the weight of aircraft components is crucial for fuel efficiency and overall performance, therefore bearings (including their components) must be designed to minimize weight without compromising strength and durability.
- CORROSION AND TEMPERATURE RESISTANCE: Because aircraft operate in a wide range of environmental conditions (including exposure to moisture, salt, other corrosive elements and extreme temperatures), components must be resistant tocorrosion and high temperature conditions to maintain their integrity over time.
- HIGH LOAD CAPACITY AND FATIGUE RESISTANCE: Bearings in aircraft applications must be capable of supporting heavy loads (both radial and axial) and of withstanding repeated stress cycles without failure, as they experience constant movement and load changes during flight.
- LONGEVITY: Bearings in aircraft are expected to have a long service life with minimal maintenance, so also components must be designed and manufactured to withstand extended periods of use without degradation.
- REGULATORY COMPLIANCE: All components used in aircraft bearings mus t meet s tringent regulatory standards set by aviation authorities.
- QUALITY CONTROL AND TRACEABILITY: Rigorous quality control measures are essential to ensure the consistency and reliability of these bearings’ components, therefore full traceability of materials and manufacturing processes is crucial point for quality assurance.
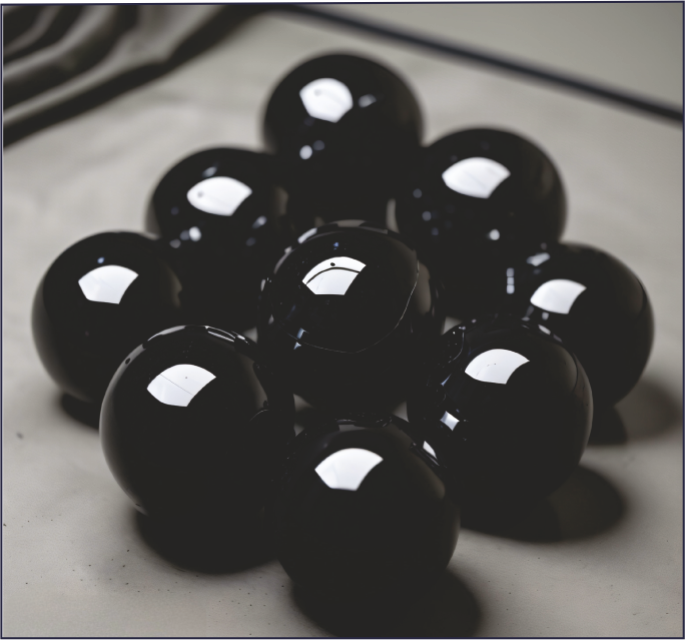
Overall, the components used in aircraft bearings are engineered to the highest standards to ensure the safety, performance, and reliability of aircraft in various operating conditions. ICT can offer balls, rings and cages for aircraft bearings thanks to its manufacturing partners in Europe, America and Asia, who all adhere to strict quality control and certification proce s s e s to me et the above requirements.
Steel balls, rollers and rings, for instance, are offered by ICT in steels like M50 AMS6491, AISI 52100 AMS6440 and AMS 6444, with VIM (Vacuum Induction Melting) and VAR (Vacuum Arc Remelt) process.
Balls are also offered in silicon nitride Si3N4 (as well as rollers), zirconia and tungsten carbide material. Also balls in AISI 440C stainless steel (AMS 5618 and AMS 5630) with sub-zero treatment are made available, to guarantee excellent dimensional stability up to temperature of 150°C.
All balls meet the stringent requirements of aerospace industry and are available in the range from 2 to 63.5 mm diameter. Steel balls are 100% eddy-current inspected and all metrological, metallurgical and raw material certifications are provided to customers together with products. NADCAP qualified heat treatment, material sorting, particles control, nital etching and fluorescent penetrant inspection can all be performed.
Cages for aircraft bearings have to be produced in special materials in order to meet the stringent application conditions. ICT provides them in C93200 per SAE J462 or ASTM B584, C93700 per SAE J462 or ASTM B584 and 4340 AMS 6414 or AMS 6415, even in small batches.